4 Function Non-Slam Air Release Valves
Home » 4 Function Non-Slam Air Release Valves
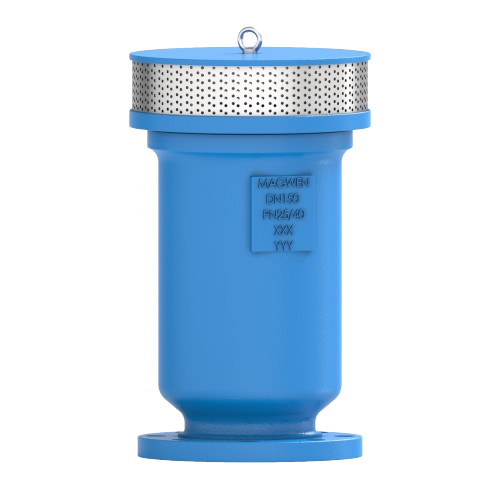
4 Function Non-Slam Air Release Valves
Air Release Valves serve two main purposes:
- Release trapped air pockets present in pipelines.
- Re-introduce air into the pipeline when flow rates drop/pumping is halted.
Older generations of Air Release Valves feature bulky designs, with singular functionality – this meant that end users would have to accommodate this bulk and install multiple valves for release and reintroduction of air to secure their pipelines.
Magwen Air Release Valves features 4 Function, Non-Slam operation in a single, lightweight and compact package. The 4 functions executed are:
- Release of large volumes of high velocity air out from pipelines during initial stages of pumping
- Release of air pockets featuring smaller volumes and low velocity that may develop during regular operation.
- Reintroduction of air into pipelines when pumping stops and line media is drained (prevents damage due to vacuum pockets).
4 Function Non-Slam operation – reduces back flow velocity of the media column and weakens Water Hammer effect.
Additionally, Magwen’s Air Release Valves offer users the following advantages:
- Compact single chamber design.
- Tamper-proof, anti-theft construction for enhanced line security.
- Jamming free and maintenance free operation using lightweight, self centering polypropylene floats.
- Complete protection from corrosion through effective material selection and full in-house fusion bonded epoxy coating.
Size Range: NPS 0.5” – 12” | DN15 – DN300
Pressure Ratings: Up-to PN40 | Up-to #300
Material choices: Ductile Iron, Carbon Steel, Stainless Steel
Page Under Development
Home » 4 Function Non-Slam Air Release Valves
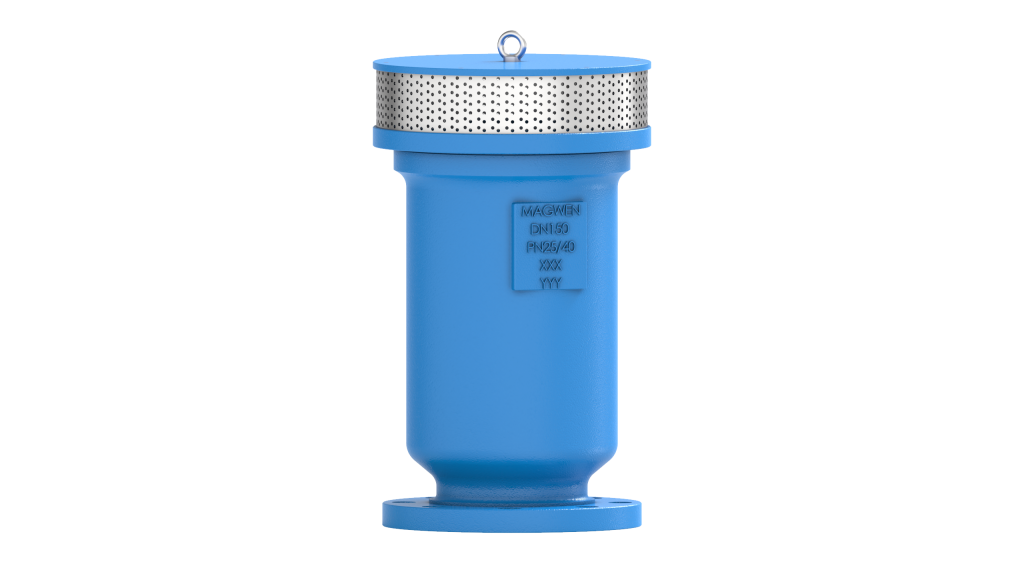
4 Function Non-Slam Air Release Valves
The triple offset butterfly valve is the most advanced form of the butterfly valve. Featuring Zero Friction triple offset geometry, the valve delivers extremely reliable sealing performance with enhanced usable product life. Enhanced metal to metal seating combined with a variety of construction material options, make this valve an excellent choice for flow isolation & control applications in a number of industries, including water infrastructure, oil and gas value chains, petrochemicals, metals processing, chemical processing, general industrial applications, extreme (low and high) temperature applications, hydrogen production, etc.
Magwen’s triple offset butterfly valve range comes equipped with design features that maximize user value by – extending service life, reducing maintenance frequency and down times, reducing cost of ownership, ensuring fire safety*, and eliminating fugitive emissions
Note: Fire safety in triple offset butterfly valves is offered by Magwen Valves Pvt Ltd in metal seated design ONLY.
Size Range: NPS 4” – 60” | DN100 – DN1500
Pressure Rating: Up-to PN420 | Up-to #2500
Materials available: Ductile Iron, Carbon Steels, Stainless Steel grades, Exotic Alloys (other materials available on request)
Body Construction: Top-Entry design, Side-Entry design
End Connection: Double Flanged, Lug Body, Wafer Type, Butt-weld end (other end connections available on request)
For more detailed technical information, please download the Product Catalog.

Two offsets relate to the shaft’s position – 1st, the shaft is made offset from the disc’s sealing plane. 2nd, the shaft is made offset from the pipe’s centreline. The third offset relates to the sealing cone’s geometry – the apex of the sealing cone is made angularly offset from the pipe centreline. The result – Zero Friction operation, enhanced seal reliability and useable life. Also makes it possible to use metal – metal sealing.
The valve can be provided with either a metal seat, or a soft PTFE seat. In metal seated design, a Stellite-21 weld overlay is provided for enhanced resistance to wear and corrosion at higher temperatures. In soft seated design, we provide a PTFE seat ring. Using a specialized, in-house procedure the soft PTFE seat is given triple offset sealing profile to ensure tight shut off.
The seal ring is made of metal + graphite sheet laminates by default. The laminated design allows the seal ring to flex and assume the shape of the valve seat. Optionally, metal sheet laminate and solid design seal rings are also available.
The disc is given a slim profile to minimize pressure drops and maximize flow through the valve.
ISO Top Flange Bracket:
To mount operators, a bracket is provided that is designed as per ISO 5211. This maximizes compatibility with operator types and allows for easy assembly and disassembly during maintenance, switching operators, etc.
On either shaft end, provisions are provided that secure the shaft in place and prevent shaft ejection under elevated line pressure.
The shaft ends are provided with redundant and fire safe sealing to prevent contact between line media and shaft bearings, enhancing their usable life and preventing jamming.
Fugitive emissions from the shaft bores are prevented by ‘live loading’ the packing material using Belleville washers.
The shaft and disc are mated using keyways, which minimizes hysteresis. Axial movement of the disc along the pipe and along the shaft is locked using precisely machined fasteners.
A dimple is provided in the drive end side of the shaft that makes clear the position of the disc at any given time.